بتن سیمانی پرتلند معمولاً مقاومت خوبی در برابر اسیدها ندارد. با این حال، برخی از اسیدهای ضعیف را می توان تحمل کرد، به ویژه اگر قرار گرفتن در معرض گاه به گاه باشد. اساساً سه راه برای بهبود مقاومت بتن در برابر اسیدها وجود دارد،انتخاب ترکیب مناسب بتن برای نفوذناپذیری تا حد امکان، جداسازی آن از محیط با استفاده از پوشش مناسب یا اصلاح محیط برای ساخت. نسبت به بتن تهاجمی کمتری دارد. اسیدها با حل کردن ترکیبات سیمانی هیدراته و بدون هیدراته و همچنین سنگدانه های آهکی به بتن حمله می کنند. در بیشتر موارد، واکنش شیمیایی ترکیبات کلسیم محلول در آب را تشکیل می دهد که سپس شسته می شوند. سنگدانه های سیلیسی در برابر اکثر اسیدها و سایر مواد شیمیایی مقاوم هستند و گاهی اوقات برای بهبود مقاومت شیمیایی بتن مشخص می شوند.
زوال بتن با کاهش pH اسید از 6.5 افزایش می یابد. در واقع، هیچ بتن سیمانی هیدرولیک، صرف نظر از ترکیب آن، اگر در معرض محلولی با pH 3 یا کمتر قرار گیرد، برای مدت طولانی دوام نمی آورد. برای محافظت از بتن در برابر چنین محیط های شدید اسیدی، اغلب از عملیات سطحی استفاده می شود. درمانهای زیادی در دسترس هستند. بتن مقاوم در برابر مواد شیمیایی محصولی منحصر به فرد است که دارای مزایا و کاربردهای متعددی برای مشاغلی است که با مواد شیمیایی و اسیدهای خطرناک کار می کنند. دو نوع بتن مقاوم در برابر اسید وجود دارد، بتن گوگردی و بتن سیلیکات. سولفورکریت از مخلوطی از سنگدانه و سیمان گوگرد مذاب ساخته شده است. بتن سیلیکات یک بتن پلیمری دو جزئی مقاوم در برابر اسید معدنی است که بر اساس شیمی سیلیکات پتاسیم ساخته شده است. به خوبی شناخته شده است که بتن در برابر اسیدها مقاومت چندانی ندارد. به خصوص تماس بین بتن و اسید سولفوریک که اسید بسیار قوی است، اغلب منجر به نوع شدید خوردگی بتن می شود. به عنوان مثال دیواره های لوله های بتنی فاضلاب که در تماس با خاک های غنی از سولفات هستند ممکن است در اثر این نوع خوردگی خراب شوند. به دلیل عملکرد باکتری های کاهنده سولفات، سولفات های موجود در خاک می توانند به سولفید تبدیل شوند که می توانند با آهن ترکیب شوند و پیریت ها را تشکیل دهند.
هنگامی که اکسیژن و آب در دسترس باشد، پیریت به سولفات آهن تبدیل می شود و اسید سولفوریک تشکیل می شود. واکنش بین اسید سولفوریک و هیدروکسید کلسیم در بتن منجر به تشکیل گچ می شود. این با افزایش حجم با ضریب 1.2 تا 2.2 همراه است. گچ تشکیل شده بیشتر با هیدرات آلومینات کلسیم موجود در بتن واکنش می دهد. محصول واکنش کانی اترینگیت است که حجمی چند برابر بیشتر از حجم ترکیبات اولیه دارد. بنابراین تشکیل اترینگیت انبساط حجم زیادی ایجاد می کند که منجر به افزایش فشار داخلی و متعاقب آن خراب شدن بتن می شود. در ادبیات، تأثیر مثبت اصلاح پلیمر بر دوام بتن قبلاً ذکر شده است. افزودن یک لاتکس پلیمری به مخلوط بتن تازه، در حین هیدراتاسیون سیمان، بسته به ظرفیت تشکیل لایه پلیمر اضافه شده و مقدار پلیمر اضافه شده، منجر به تشکیل یک لایه کم و بیش پیوسته می شود.
وجود لایه پلیمری منجر به تغییراتی در خواص ریزساختار بتن می شود که بر دوام آن تأثیر می گذارد. اگرچه تغییرات به نوع و مقدار پلیمر مورد استفاده بستگی دارد، به طور کلی تأثیرات مثبت گزارش شده است. از آنجایی که تأثیر بر ساختار منافذ در بیشتر موارد منجر به کاهش حجم منافذ بزرگتر (شعاع > 0.2 میکرومتر) همراه با افزایش منافذ کوچکتر (شعاع کمتر از 0.075 میکرومتر) می شود، این منجر به پالایش منافذ می شود. به دلیل وجود فیلم پلیمری، برخی از منافذ پر یا مهر و موم می شوند تا دیگر در انتقال گاز، بخار یا مایعات از طریق بتن شرکت نکنند. اکثر پلیمرها دارای برخی کیفیت های کاهش دهنده آب هستند به طوری که برای کارایی هدف معین می توان از نسبت w/c کمتری استفاده کرد که همچنین منجر به کیفیت بتن بالاتر می شود. اثرات ذکر شده در بالا، مشخصه برای بتن اصلاح شده پلیمری، کاهش قابل توجهی در نفوذپذیری بتن اصلاح شده ایجاد می کند. تحقیقات زیادی نشان داده است که سطح مشترک سنگدانه ها و خمیر سیمان یکی از آسیب پذیرترین قسمت های خمیر سیمان در مورد حمله شیمیایی نیز می باشد. تغییرات پلیمری به عملکرد بهتر منطقه انتقال نشان می دهد. کیفیت ناحیه انتقال به دلیل غلظت نسبتاً بالای ذرات پلیمری در این ناحیه و/یا به دلیل اثر پل بین خمیر سیمان و سنگدانه ها بهبود یافته است. علاوه بر این، اصلاح پلیمر باید تأثیر مثبتی بر ساختار محصولات هیدراتاسیون داشته باشد. ساختار آمورف تر، با مقدار کمتری از کریستال های بزرگ تشکیل می شود. این به مقاومت مکانیکی بتن و همچنین مقاومت شیمیایی محصول هیدراتاسیون کمک می کند . تمام این جنبه ها باید بتن اصلاح شده پلیمری را برای استفاده در محیط های تهاجمی شیمیایی با توجه به حمله اسیدی مناسب تر از بتن معمولی کند. تحقیقات مختلف قبلاً تأثیر مفید پلیمرها بر مقاومت شیمیایی بتن را تأیید کرده است. اثر مثبت با توجه به اسیدهای آلی مانند اسید لاکتیک و استیک در آزمایشات قبلی نشان داده شده است. همچنین به دلیل افزودن پلیمر استایرن بوتادین و پلیمر اکریلیک استایرن در آزمایشات با استفاده از محلول های اسید سولفوریک با مقادیر pH متفاوت، عملکرد بهتری پیدا کردند.
اکثر محققان این عقیده را دارند که ایجاد یک بتن با کیفیت خوب، با کاهش تخلخل، در بیشتر موارد دوام کلی بتن را بهبود می بخشد. کاهش تخلخل بتن را می توان به روش های مختلف به دست آورد: استفاده از نسبت w/c کم، استفاده از فوق روان کننده ها، استفاده از افزودنی های معدنی مانند خاکستر بادی و دوده سیلیس. مزایای کلی در مورد ساختار خمیر سیمان به دلیل استفاده از دوده سیلیس به خوبی شناخته شده است. همه تحقیقات تأثیر مثبتی بر توزیع اندازه منافذ نشان میدهند. افزایش منافذ کوچک و کاهش منافذ بزرگ منجر به اصلاح ساختار منافذ می شود. اگرچه کاهش تخلخل کل در همه تحقیقات تایید نشده است، در بیشتر موارد کاهش نفوذپذیری مشاهده. به طور کلی می توان بیان کرد که افزودن دوده سیلیس منجر به بتن با ساختار متراکم تر می شود. علاوه بر این، افزودن دوده سیلیس منجر به کاهش یا حذف کامل هیدروکسید کلسیم آزاد و قابل شستشو می شود. علیرغم تمام آن جنبه های مثبت، استفاده از دوده سیلیس، در صورت وجود خطر حمله سولفات، موضوع بحث و مناقشه است. بسیاری از محققان نتایج مثبتی در مورد دوام بتن در معرض حمله سولفات با افزودن دوده سیلیس به مخلوط بتن یافته اند. عملکرد بهتر آن مخلوط ها بیشتر به اصلاح ساختار منافذ، کاهش نفوذپذیری و کاهش محتوای هیدروکسید کلسیم نسبت داده شد. دورنینگ و همکاران گزارش داد که خمیر هیدرات سیلیکات کلسیم تشکیل شده با دوده سیلیس باید در محیط های با pH پایین پایدارتر باشد، که همچنین به عملکرد بهتر بتن کمک می کند.
در این رابطه تیلور نیز اشاره کرد که استفاده از دوده سیلیس منجر به ایجاد ساختار یکنواخت تری از فاز هیدرات سیلیکات کلسیم می شود. سایر اثرات مثبت دوده سیلیس باید نسبت C/S کمتر در هیدرات های سیلیکات کلسیم باشد که شامل امکان ترکیب مقدار بیشتری از آلومینیوم است، بنابراین میزان آلومینیوم موجود برای تشکیل اترینگیت را کاهش می دهد. از سوی دیگر، برخی از تحقیقات اثر مثبت کمتر یا بدون اثر مثبت افزودن دوده سیلیس را با توجه به حمله سولفات نشان میدهند. نویل اظهار داشت که در صورت حمله سولفات، تأثیر دوده سیلیس مبهم است. تالرودریافت که تشکیل اترینگیت مرتبط با واکنش پوزولان ها بسیار سریعتر از محصولات هیدراتاسیون معمولی رخ می دهد. این منجر به افزایش نرخ خوردگی شد. برای بررسی بهبود احتمالی ناشی از افزودن دوده سیلیس، یک مخلوط با افزودن 6/8 درصد دوده سیلیس بر حسب وزن سیمان ساخته شد. این مخلوط همچنین با هدف ایجاد بتن بسیار متراکم ساخته شده است تا این اثر با نفوذ کمتر اسید به داخل بتن، دوام را بهبود بخشد. مخلوط دوده سیلیس با افزودن 30 کیلوگرم بر متر مکعب دوده سیلیس به مخلوط مرجع ساخته شد. نسبت w/c کم (0.34) این مخلوط همراه با افزودن مقدار زیادی فوق روان کننده، بتن بسیار متراکم و قابل کار خوبی را ایجاد کرد.
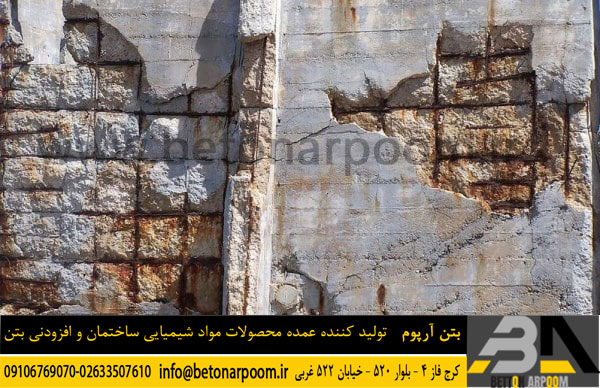
محققان آلمانی تلاش کردند تا مقاومت لوله های بتنی در معرض حملات اسیدی طولانی مدت را در محدوده PH بین 4.5 تا 6.5 بهبود بخشند. راه حل اساسی افزایش مقاومت شیمیایی با کاهش نفوذپذیری بتن برای بهینه سازی طرح های مخلوط بتن استفاده شد. هدف این بود که نرخ فرسایش آنقدر پایین نگه داشته شود که بتوان عمر مفیدی در حدود 100 سال به دست آورد. مشخص شد که بهبود قابل توجهی در مقاومت اسیدی را می توان با استفاده دقیق کنترل شده از مواد سیمانی تکمیلی خوب به دست آورد. دلیل اصلی افزایش مقاومت اسیدی بتن مورد بررسی، تشکیل خمیر سیمان سخت شده بسیار متراکم و سطح مشترک سنگدانه با تخلخل بسیار کم بود. استفاده از سیمان سرباره باعث افزایش مقاومت اسیدی و همچنین سیمان های پرتلند با دوده سیلیس (تا 8 درصد جرمی مواد سیمانی) یا خاکستر بادی شد.
کربناته شدن از طریق تماس با آب: آبهای طبیعی معمولاً دارای pH بیش از 7 و به ندرت کمتر از 6 هستند. حتی آبهایی با PH بیشتر از 6.5 نیز اگر حاوی بی کربنات باشند ممکن است تهاجمی باشند. هر آبی که حاوی یون بی کربنات باشد همچنین حاوی دی اکسید کربن آزاد است که می تواند کربنات کلسیم را حل کند مگر اینکه از قبل اشباع وجود داشته باشد. آب با این دی اکسید کربن تهاجمی با واکنش اسیدی عمل می کند و می تواند به بتن و سایر محصولات سیمان پرتلند، خواه گازدار باشند یا نه، حمله کند. یک مشخصات آلمانی، DIN 4030، شامل معیارها و یک روش آزمایشی برای ارزیابی پتانسیل آسیب ناشی از آب حاوی اسید کربنیک است.
مقاومت در برابر خوردگی: مقاوم در برابر اسید و نمک و در تاسیساتی که تجهیزات سنگین ممکن است به سطح بتن آسیب برساند بسیار مفید است. این یک بتن مقاوم در برابر مواد شیمیایی است که در مقابل باکتری ها نیز مقاوم است.
قدرت بیشتر: خواص مقاومتی برابر یا بیشتر از بتن معمولی. این شامل مقاومت فشاری، کششی و خمشی است.
2.2 تست های مکانیکی
اسلامپ (NBN B15-232، 1982)، جریان (NBN B15-233، 1982)، چگالی ظاهری (NBN B15-213، 1982) و محتوای هوا (NBN B15-224، 1970) بتن تازه بود. در طول تولید مخلوط های مختلف اندازه گیری می شود. مقاومت فشاری (NBN B15-220، 1990) و جذب آب (NBN B15-215، 1989) در 28 روز برای هر مخلوط روی 3 مکعب (158 x 158 x 158 میلی متر) تعیین شد. 2.3 روش آزمایش شیمیایی تسریع شده مقاومت ترکیبات مختلف بتن در برابر حمله اسید سولفوریک با یک دستگاه آزمایش برای آزمایشهای تخریب تسریع شده (TAP) بررسی شد. توضیحات دقیق تری از روش آزمون مورد استفاده توسط De Belie و همکاران ارائه شده است. [34]. در طول آزمایش شیمیایی برای هر مخلوط، سه سیلندر (Ø 270 mm، h = 70 mm) تحت یک روش حلقوی غوطهوری در محلول اسید سولفوریک 0.5٪ قرار گرفتند و توسط هوا خشک شدند. سیلندرها که روی محورهای افقی ثابت شده بودند، با سرعت 1 دور در ساعت از طریق گیرنده های جداگانه می چرخیدند. هر نقطه از محیط بیرونی در طول 1/3 زمان چرخش غوطه ور شد. پس از هر چرخه، که به مدت 12 روز به طول انجامید، سیلندرها با برس های چرخشی مسواک زده می شدند تا ذرات بتن ضعیف چسبیده حذف شوند. خوردگی نمونه ها با استفاده از حسگرهای لیزری متصل به کامپیوتر اندازه گیری شد. از این اندازه گیری ها می توان تغییر شعاع سیلندرهای مختلف را محاسبه کرد. اندازه گیری ها قبل و بعد از مسواک زدن سیلندرها انجام شد. به این ترتیب میتوان میانگین تغییر شعاع استوانهها را در اثر واکنش شیمیایی بتن با محلول اسید سولفوریک در حین غوطهوری و همچنین تغییر شعاع ناشی از عمل مکانیکی برس زدن سیلندرها تعیین کرد. انبساط زیاد بتن در نتیجه دوره غوطه وری همیشه باعث اتلاف زیاد مواد در اثر برس زدن نمی شود و بالعکس. بنابراین از آنجایی که همیشه رابطه روشنی بین دو پارامتر وجود نداشت، کمی کردن هر دو پارامتر برای مشاهده کل فرآیند خوردگی ضروری بود.
تست های مکانیکی: اسلامپ، جریان، چگالی ظاهری و محتوای هوا بتن تازه بود. در طول تولید مخلوط های مختلف اندازه گیری می شود. مقاومت فشاری و جذب در 28 روز برای هر مخلوط روی 3 مکعب تعیین شد. روش آزمایش شیمیایی تسریع شده مقاومت ترکیبات مختلف بتن در برابر حمله اسید سولفوریک با یک دستگاه آزمایش برای آزمایشهای تخریب تسریع شده بررسی شد. توضیحات دقیق تری از روش آزمون مورد استفاده توسط De Belie و همکاران ارائه شده است. در طول آزمایش شیمیایی برای هر مخلوط، سه سیلندر تحت یک روش حلقوی غوطهوری در محلول اسید سولفوریک 0.5 % قرار گرفتند و توسط هوا خشک شدند. سیلندرها که روی محورهای افقی ثابت شده بودند، با سرعت 1 دور در ساعت از طریق گیرنده های جداگانه می چرخیدند. هر نقطه از محیط بیرونی در طول 1/3 زمان چرخش غوطه ور شد. پس از هر چرخه، که به مدت 12 روز به طول انجامید، سیلندرها با برس های چرخشی مسواک زده می شدند تا ذرات بتن ضعیف چسبیده حذف شوند. خوردگی نمونه ها با استفاده از حسگرهای لیزری متصل به کامپیوتر اندازه گیری شد. از این اندازه گیری ها می توان تغییر شعاع سیلندرهای مختلف را محاسبه کرد. اندازه گیری ها قبل و بعد از مسواک زدن سیلندرها انجام شد. به این ترتیب میتوان میانگین تغییر شعاع استوانهها را در اثر واکنش شیمیایی بتن با محلول اسید سولفوریک در حین غوطهوری و همچنین تغییر شعاع ناشی از عمل مکانیکی برس زدن سیلندرها تعیین کرد. انبساط زیاد بتن در نتیجه دوره غوطه وری همیشه باعث اتلاف زیاد مواد در اثر برس زدن نمی شود و بالعکس. بنابراین از آنجایی که همیشه رابطه روشنی بین دو پارامتر وجود نداشت، کمی کردن هر دو پارامتر برای مشاهده کل فرآیند خوردگی ضروری بود. اندازه گیری با حسگرهای لیزری نیز برای محاسبه زبری سطح بتن پس از برس زدن سیلندرها استفاده شد. این مقدار با تعیین خطی که میانگین نیمرخ اندازه گیری شده را نشان می دهد و شمارش تمام سطوح بین آن خط و نمایه اندازه گیری شده محاسبه شد. تقسیم این مجموع بر طول خط خاص (از طول مرجع 50 میلی متر استفاده شد) مقدار Ra را به دست می دهد.
نتایج و بحث
خواص مخلوط بتن تازه: افزودن پلیمرهای مختلف باعث افزایش ادغام هوا در مخلوطهای تازه شد. این منجر به چگالی کمتر این مخلوط ها در مقایسه با مخلوط مرجع بدون پلیمر شد. مخلوط با پلیمر استایرن بوتادین، پلیمر استایرن-اکریلیک استر و وینیلکوپلیمر دارای محتوای هوا بود که تنها 1 تا 2 درصد بیشتر از محتوای هوای مخلوط مرجع بود. با این حال، مخلوط با پلیمر اکریلیک دارای محتوای هوای 10٪ پلیمر اکریلیک و 17٪ پلیمر اکریلیک بود. محتوای هوا و چگالی مخلوط با دوده سیلیس و مخلوط با سیمان کوره بلند از همان درجه بزرگی مخلوط مرجع بود. با وجود نسبت w/c کم (0.34) مخلوط با دوده سیلیس، بتن قابل کار بسیار خوبی با اسلامپ کلاس S3 به دست آمد که به دلیل افزودن مقدار زیادی فوق روان کننده است. فقط برای مخلوط با افزودن پلیمر اکریلیک، مقدار آب محاسبه شده بر اساس نسبت w/c فرضی 0.4 برای ایجاد یک بتن قابل کار کافی بود. کارایی این مخلوط نه تنها مستقیماً تحت تأثیر افزودن پلیمر بود، بلکه به طور غیرمستقیم تحت تأثیر افزایش محتوای هوا از طریق اصلاح پلیمر بود. برای مخلوط های دیگر باید آب بیشتری اضافه کرد. برای مخلوط با پلیمر استایرن بوتادین و پلیمر استایرن-اکریلیک استر یک نسبت w/c ساختگی به ترتیب 0.42 و 0.43 برای به دست آوردن اسلامپ کلاس S1 باید استفاده می شد. افزایش نسبت w/c ساختگی به 0.48 برای مخلوط با وینیلکوپلیمر مورد نیاز بود. برای این مخلوط آب اضافه شد تا زمانی که یک اسلامپ کلاس S2 به دست آمد زیرا حتی با اسلامپ کلاس S1 بتن به دلیل چسبندگی مخلوط قابل کار نبود.
استحکام فشاری و جذب آب مخلوط های مختلف
مقادیر مقاومت فشاری و جذب آب مخلوط های مختلف بتن تعیین شده در 28 روز در جدول 3 نشان داده شده است. اصلاح پلیمری بتن منجر به کاهش مقاومت فشاری نسبت به مخلوط مرجع شد. کمترین مقدار برای مخلوط با پلیمرهای اکریلیک اندازه گیری شد. کاهش استحکام 60 و 35 درصد برای مخلوط با پلیمرهای A1 و A2 به ترتیب اندازه گیری شد. مخلوط با افزودن دوده سیلیس دارای استحکام فشاری متوسط 6/84 نیوتن بر میلیمتر مربع بود که به طور قابلتوجهی بالاتر از مخلوط مرجع بود. یون برای همه مخلوط ها، به استثنای مخلوط با پلیمر اکریلیک A1 تعیین شد. اگرچه اصلاح پلیمری بتن برای کاهش جذب آب شناخته شده است، در حقیقت افزودن پلیمر باعث ایجاد دو پدیده متضاد در مورد جذب آب می شود. از یک طرف پلیمر مانعی برای جذب آب میسازد، اما از طرف دیگر افزودن پلیمر اغلب با افزایش محتوای هوای بتن تازه همراه است. این به معنی تخلخل بالاتر است که اغلب منجر به جذب آب بیشتر می شود. بسته به مقدار هوای موجود در بتن همراه با چندین عامل دیگر (مانند درجه هیدراتاسیون سیمان، درجه تشکیل لایه پلیمر)، اصلاح پلمر همچنان می تواند منجر به جذب آب کمتر شود. در مورد پلیمر اکریلیک A1، جذب آب بالای این مخلوط بتن احتمالاً به دلیل محتوای فوق العاده بالای هوای بتن تازه است. چنین محتوای بالای هوا باید تخلخل بالایی ایجاد کند که در جذب آب بالا منعکس می شود. همین پدیده، اما در نسبتهای کمتر، برای مخلوط با پلیمر اکریلیک محتوای هوا 9.7٪، جذب آب 2.28٪ و مخلوط با وینیلکوپلیمر محتوای هوا 5.2٪، جذب آب 2.71٪ مشاهده شد. مخلوط با پلیمر استایرن-اکریلیک استر و پلیمر استایرن بوتادین جذب آب کمتری نسبت به مخلوط مرجع داشتند. مخلوط با افزودن دوده سیلیس در واقع بتن بسیار متراکمی را ایجاد کرد که میانگین جذب آب آن تنها 1.78٪ بود.
آزمایش شیمیایی با اسید سولفوریک: از آنجایی که مخلوط با پلیمر اکریلیک نتایج پایینتری در مورد محتوای هوا، مقاومت فشاری و جذب آب نشان داد، در آزمایش شیمیایی در نظر گرفته نشد. در شکل 1 میانگین تغییر شعاع سیلندرها در مقابل تعداد اندازه گیری ها برای مخلوط های مختلف بتن نشان داده شده است. برای هر چرخه دو اندازه گیری انجام شد: یکی قبل و دیگری بعد از مسواک زدن سیلندرها. مقدار مثبت نشان دهنده انبساط سیلندر در مقایسه با اندازه اولیه است، در حالی که مقدار منفی به این معنی است که به دلیل از دست دادن مواد، شعاع سیلندر نسبت به ابعاد اولیه کاهش یافته است. افزایش و کاهش متناوب در شعاع مربوط به انبساط متناوب بتن به دلیل غوطه وری و تشکیل محصولات واکنش و متعاقب آن از دست رفتن مواد در اثر برس زدن است. در نهایت کاهش شعاع می تواند در طول دوره غوطه ور شدن سیلندرها به دلیل از بین رفتن چسبندگی قطعات منبسط شده نیز رخ دهد. تجزیه و تحلیل آماری بر روی نتایج پس از مسواک زدن (حتی اندازهگیریها در شکل 1) با استفاده از آزمون Student-NewmanKeuls با سطح معنیداری 05/0 انجام شد. در چهار چرخه اول، چند تفاوت قابل توجه مشاهده شد. از سیکل پنجم، مخلوط های مختلف را می توان در حداقل دو گروه طبقه بندی کرد. یک گروه شامل مخلوط مرجع، مخلوط با سیمان کوره بلند و مخلوط با پلیمر استایرن اکریلیک استر و وینیل کوپلیمر بود. گروه دیگر شامل مخلوط با پلیمر اکریلیک و پلیمر استایرن بوتادین و مخلوط با دوده سیلیس بود. مخلوط های گروه دوم بیشترین آسیب پذیری را نسبت به تخریب داشتند. در حال حاضر پس از سه و پنج چرخه کاهش شعاع به ترتیب برای مخلوطهای با دوده سیلیس و پلیمر استایرن-بوتادین و مخلوط با پلیمر اکریلیک مشاهده شد. مخلوط مرجع و مخلوط با وینیلکوپلیمر تنها پس از هشت چرخه یک مقدار منفی (کاهش در شعاع در مقایسه با شعاع اولیه) نشان دادند. از سوی دیگر، مخلوط با سیمان کوره بلند و پلیمر استایرن-اکریلیک استر پس از 9 سیکل هنوز یک مقدار مثبت نشان دادند به این معنی که ابعاد سیلندرها هنوز بزرگتر از سیلندرهای اولیه بودند. برای مخلوط با سیمان کوره بلند، تفاوت با شعاع اولیه تنها 0.1 میلی متر بود. برای مخلوط با پلیمر استیرن-اکریلیک استر، انبساط نمونه بتن 1.2 میلی متر (افزایش شعاع با 0.6 میلی متر) اندازه گیری شد. پس از 9 چرخه تفاوت معنی داری بین مخلوط با پلیمر استایرن-اکریلیک استر، مخلوط با سیمان کوره بلند و مخلوط با وینیلکوپلیمر وجود داشت. همه آن مخلوط ها تفاوت معنی داری در تغییر شعاع متوسط نشان دادند. از طرف دیگر مخلوط مرجع به گروه دوم اضافه شد. از این رو، تفاوت معنی داری بین مخلوط مرجع، مخلوط با دوده سیلیس، مخلوط با پلیمر اکریلیک و مخلوط با پلیمر استایرن- بوتادین مشاهده نشد.
این مقادیر مجموع تمام تفاوتهای بین مقادیر شعاع اندازهگیری شده پس از مسواک زدن و مقادیر شعاع اندازهگیری شده قبل از تمیز کردن چرخه بعدی را نشان میدهند. از این رو، اثر تمیز کردن منتفی است. تفاوت های کمتر معنی داری بین مخلوط های مختلف پیدا شد. مخلوط با دوده سیلیس بیشترین انبساط تجمعی را نشان داد و این عمدتاً به دلیل انبساط پس از چرخه های 2، 3 و 4 بود. از طرف دیگر مخلوط با سیمان کوره بلند انبساط نسبتاً کمی را نشان داد. پس از نه چرخه افزایش تجمعی در شعاع تنها 0.2 میلی متر اندازه گیری شد. همه مخلوط های اصلاح شده پلیمری، به استثنای مخلوط با پلیمر اکریلیک، انبساط بیشتری نسبت به مخلوط مرجع نشان دادند. برای مخلوط با پلیمر اکریلیک پس از غوطه وری متناوب چرخه های 6، 7 و 8 هیچ انبساط اندازه گیری نشد. احتمالاً انبساط بتن صورت گرفته است اما مواد منبسط شده چسبندگی کافی نداشته و قبلاً سقوط کرده است. در مرحله غوطه وری با توجه به این پدیده، انبساط نشان داده شده در شکل 2 حداکثر انبساط رخ داده نیست، بلکه یک دست کم برآورد است. شکل 3 تغییرات تجمعی شعاع متوسط مخلوط های مختلف را به دلیل برس زدن سیلندرها نشان می دهد. این مقادیر نشان دهنده مجموع تمام تفاوت های بین مقادیر شعاع اندازه گیری شده قبل از مسواک زدن و مقادیر شعاع اندازه گیری شده پس از مسواک زدن در همان چرخه است. از این رو فقط تاثیر مسواک زدن در نظر گرفته می شود. بیشترین تلفات تجمعی مواد برای مخلوط با دوده سیلیس اندازه گیری شد. از چرخه های 2 تا 6 کاهش میانگین تغییر شعاع سیلندرهای مخلوط های مختلف بتن در برابر تعداد اندازه گیری ها. شعاع با 0.2 تا 0.3 میلی متر در هر سیکل اندازه گیری شد. برای چرخه های زیر کاهش متوسط تری مشاهده شد.
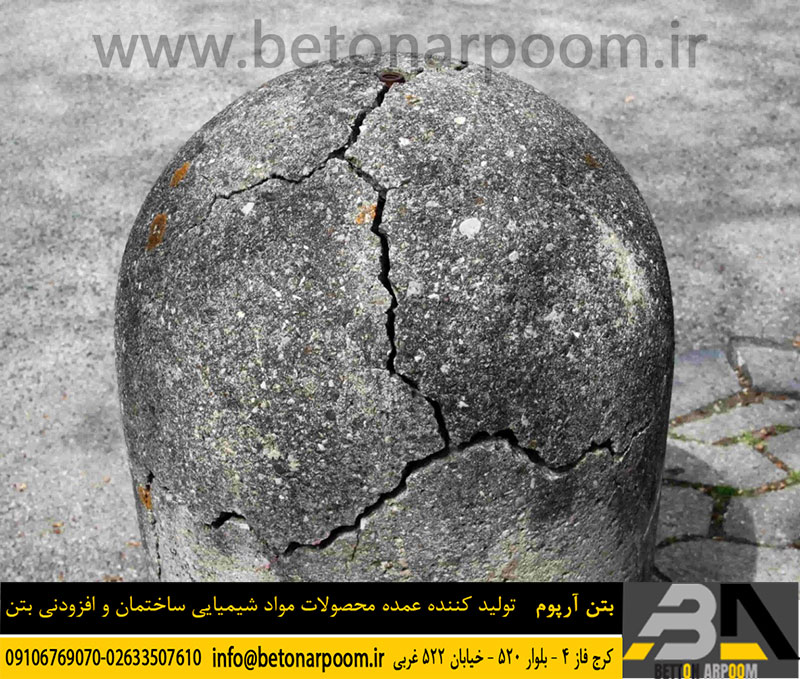
از چرخه 2 مخلوط با پلیمر استایرن-بوتادین نیز مقاومت کمتری در برابر عمل مکانیکی برس زدن داشت. به دلیل کاهش فوقالعاده زیاد شعاع بعد از چرخه 5، مخلوط با پلیمر اکریلیک A2، علیرغم کاهش نسبتاً متوسط در سایر چرخهها، کاهش تجمعی 1.1 میلیمتری پس از 9 چرخه داشت. هیچ اتلاف قابل توجهی از مواد به دلیل برس زدن برای مخلوط با سیمان کوره بلند مشاهده نشد. در اغلب موارد انبساط زیاد بتن در مرحله غوطه وری با اتلاف زیاد مواد در اثر برس زدن همراه بود. بیشترین انبساط و بیشترین تلفات مواد برای مخلوط با دوده سیلیس، هر دو در طول چرخههای 2، 3 و 4 اندازهگیری شدند. یک استثنا در این پدیده برای مخلوط با پلیمر استایرن-اکریلیک استر یافت می شود. این مخلوط انبساط نسبتاً زیادی را نشان داد (1.0 میلی متر) اما از دست دادن مواد به 0.4 میلی متر محدود شد. احتمالاً این بتن اصلاحشده پلیمری توانایی افزایش یافته برای مقاومت در برابر فشارهای داخلی همراه با تشکیل محصولات واکنش گسترده را دارد. این ویژگی را می توان به قابلیت بالاتر تغییر شکل پلاستیک به دلیل ادغام پلیمر نسبت داد.
با وجود اینکه تمام خواص مکانیکی اندازه گیری شده مخلوط با دوده سیلیس در جهت یک بتن بسیار متراکم (نسبت w/c کم، جذب آب کم، استحکام بالا، چگالی بالا) نشان داده شد، نتایج آزمایش شیمیایی پایینتری برای بتن به دست آمد. آن مخلوط علیرغم این گفته کلی که دوام بتن با کاهش نفوذپذیری افزایش مییابد، این جنبه میتواند در صورت نفوذپذیری بسیار کم مانند مخلوط با دوده سیلیس اثر منفی داشته باشد. نویسندگان به دو جنبه منفی ناشی از اصلاح ساختار منافذ فکر می کنند. از یک طرف منافذ ریز احتمالاً مکش مویرگی افزایش یافته ای را ایجاد می کنند که در نتیجه محلولی به عمق بیشتری وارد بتن می شود. اگرچه مقدار کل محلول جذب شده توسط بتن بسیار کم است، اما محلولی که وارد بتن می شود بسیار تهاجمی است و به راحتی به یون های سولفات و پروتون ها تجزیه می شود. بنابراین حتی در غلظت های پایین نیز ترکیبات تهاجمی کافی برای تولید محصولات واکنش گسترده وجود دارد. به دلیل اصلاح ساختار منافذی، محلول در تماس با سطح بتن بزرگتر از زمانی است که همان مقدار محلول توسط بتن با منافذ بزرگتر گرفته می شود. هر چه سطح بتن بیشتر با محلول تماس داشته باشد، محصولات واکنش بیشتری را می توان تشکیل داد. از طرف دیگر منافذ کوچکتر فضای کمتری را برای محصولات واکنش گسترده ایجاد شده در مرحله غوطه وری ایجاد می کند. این می تواند منجر به فشارهای داخلی بالاتر و در نتیجه ترک های بیشتر شود. بنابراین در مورد مخلوط با دوده سیلیس، پالایش شدید ساختار منافذ بیشتر اثر منفی بر دوام داشت تا اثر مثبت. میانگین Ra-vale مخلوط های مختلف بتن در مقابل تعداد چرخه ها در شکل 4 نشان داده شده است. زبری اولیه، قبل از شروع آزمایش شیمیایی اندازه گیری شده، در سیکل صفر ذکر شده است. همه مخلوط ها دارای زبری سطح اولیه در همان ترتیب بزرگی (0.05 تا 0.10 میلی متر) بودند. مخلوط با سیمان کوره بلند تغییر بسیار ملایمی در زبری در تمام چرخه ها نشان داد. برای همه مخلوطهای دیگر، به استثنای مخلوط با پلیمر اکریلیک، افزایش تدریجی در طول چرخههای بعدی اندازهگیری شد. مخلوط با پلیمر اکریلیک پس از چرخه 4 اوج را نشان داد و پس از چرخه 5 و 6 زبری کاهش یافت. این پیک با انبساط زیاد بتن مطابقت دارد. فقط خمیر سیمان در معرض انبساط زیاد قرار می گیرد. سنگدانه ها توسط اسید سولفوریک مورد حمله قرار نمی گیرند و هیچ گونه انبساط نشان نمی دهند. این اختلاف احتمالاً منجر به زبری سطح بزرگ می شود که پس از چرخه 4 اندازه گیری می شود. کاهش قابل توجهی در شعاع این مخلوط اندازه گیری شد به این معنی که ماده منبسط شده حذف شد. بنابراین تفاوت بین خمیر سیمان و سنگدانه ها به این ترتیب کاهش یافت که در کاهش زبری سطح پس از سیکل های 5 و 6 نیز بیان می شود.
نتیجه گیری
اگرچه روش مورد استفاده ماهیت پدیدارشناسی داشت، اما این آزمایش ابزار بسیار مفیدی برای مقایسه مقاومت و رفتار مخلوطهای مختلف بتن در تماس با اسید سولفوریک بود. افزودن پلیمرهای انتخاب شده به بتن باعث افزایش ادغام هوای بتن تازه شد. این امر از یک سو منجر به مقادیر بالاتر اسلامپ و جریان بتن تازه و از سوی دیگر در چگالی کمتری شد. افزودن 7.5 درصد از پلیمرهای اکریلیک به وزن سیمان باعث ایجاد بتن با محتوای هوای غیرقابل قبولی شد. برای این نوع پلیمر شاید باید از غلظت های کمتری برای غلبه بر این مشکل استفاده شود. به دلیل افزودن مقدار زیادی فوق روانکننده، مخلوط با دوده سیلیس علیرغم نسبت w/c پایین (0.34) کارایی بالایی داشت (اسلامپ S3، جریان F2). همه مخلوطهای بتن اصلاحشده پلیمری آزمایششده دارای مقاومت فشاری کمتری نسبت به مخلوط مرجع بدون افزودن پلیمر بودند. بسته به نوع پلیمر، کاهش 10 تا 60 درصد در مقایسه با مخلوط مرجع اندازه گیری شد. تأثیر افزودن پلیمر بر جذب آب بتن به نوع پلیمر مورد استفاده بستگی دارد. مخلوط با دوده سیلیس مقاومت فشاری بالاتر و جذب آب کمتری نسبت به مخلوط مرجع داشت. با توجه به مقاومت مخلوط های مختلف در برابر محلول اسید سولفوریک 0.5 درصد، مخلوط ها می توانند.
به ترتیب افزایش مقاومت به شرح زیر طبقه بندی می شود:
– مخلوط با دود سیلیس
– مخلوط با پلیمر استایرن بوتادین، مخلوط با پلیمر اکریلیک (A2)
– مخلوط مرجع
– مخلوط با وینیل کوپلیمر
– مخلوط با پلیمر استایرن-اکریلیک استر
– مخلوط با سیمان کوره بلند
اگر مخلوط های مختلف با مخلوط مرجع با سیمان پرتلند مقایسه شود، باید در نظر گرفت که این مخلوط دارای کیفیت نسبتاً بالایی است (نسبت w/c کم، استحکام نسبتاً بالا، چگالی بالا، ارزش جذب آب کم). علاوه بر این، سیمانی با محتوای کم C3A بود که مقاومت بالایی در برابر تهاجم اسید سولفوریک ایجاد می کرد. افزودن پلیمرهای مختلف باعث افزایش انبساط سیلندرهای بتنی در مرحله غوطه وری در آزمایش شیمیایی شد. برای برخی از پلیمرها (پلیمر استایرن-بوتادین و پلیمر اکریلیک)، در مقایسه با مخلوط مرجع، این افزایش در انبساط با افزایش از دست دادن مواد به دلیل برس زدن همراه بود. ترکیب این دو پدیده منجر به بتن با مقاومت کمتر در برابر اسید سولفوریک شد. برعکس، برای شکل 4 - میانگین تغییر مقدار Ra مخلوط های مختلف بتن در مقابل تعداد چرخه ها. برخی از پلیمرهای دیگر (وینیل کوپلیمر و پلیمر استایرن اکریلیک استر) انبساط با افزایش از دست دادن مواد به دلیل برس زدن همراه نبود. در این مورد نتایج بهتری در مورد تغییر شعاع این نمونه ها در مقایسه با مخلوط مرجع به دست آمد. محتوای هوای کم، جذب آب کم و چگالی زیاد مخلوط با دوده سیلیس نشان دهنده این بود که این مخلوط باید نفوذپذیری پایینی داشته باشد. علیرغم این خاصیت، به نظر می رسید که این مخلوط مقاومت بسیار کمی در برابر عملکرد تهاجمی محلول اسید سولفوریک داشته باشد. انبساط زیاد سیلندرها در طول غوطه وری در ترکیب با اتلاف زیاد مواد به دلیل برس زدن اندازه گیری شد.